Industrial Applications For Various Ceramic Materials

The structure of ceramic materials is often crystalline or somewhat crystalline. They are made of non-metallic, inorganic material. Early ceramics were mostly made of clay and clay mixes, much like pottery. Natural mineral deposits of easily available clay and sand, when combined to achieve the proper consistency when mixed with various liquids, are perfect for making moldable material useful for traditional ceramics. Part of the world’s potters and bricklayers utilize this ancient ceramics combination. Because it is easily accessible, simple to combine, and affordable.
The use of ceramics in technological applications that are far more complicated than their classical ceramic materials predecessors is now possible thanks to recent breakthroughs. Modern sophisticated ceramic machining frequently utilizes the expertise of physicists, chemists, and various engineers and uses precise materials, measurements, and processes. They are employing in the production of items as basic as floor tiles and as detailed and complex as nuclear fuel pellets.

In order to produce ceramics with the qualities required to survive very dangerous environmental conditions, modern advanced ceramics relies on high-quality materials rather than only sand and clay. However, in order for faults to be clearly obvious, these same ceramics must produce with extreme accuracy.
The majority of classic ceramics are renewing for their strength, brittleness, and hardness. Because porcelain resists the passage of electricity, traditional ceramics have historically been employed as electrical insulators. Modern industrial ceramics may produce to be just as durable and conductive as the toughest metals. These ceramics crafts with such accuracy that their fundamental cellular structure is managed, generated, and controlled. Superconductors and several other sorts of advanced mechanical devices frequently employ such extremely conductive ceramic materials. This makes these heat-conductive ceramics a very valuable commodity. Sevgili tadında görüşme yapan kadınlar eskort sayfasında sizi bekliyor.
Ceramics fall into one of three broad categories: oxides, non-oxides, or composites. This article examines the many forms of ceramics and deconstructs those categories.
Different Oxide Ceramics
The addition of oxide fibers to a ceramic mixture can increase the final component’s resistance to oxidation and give additional reinforcement and strength. Despite the fact that they come in a variety of compositions and can create using various techniques. All oxide fibers are initially created, often by a chemical procedure, and are then heated to complete the ceramic. Sol-gel, which involves spinning fibers from a liquid chemical solution, and polymer pyrolysis, a chemical deposition process that takes place at high heat, are two popular techniques.
Ceramic oxide fibers usually contain mixtures of titanium dioxide, zirconium dioxide, and aluminum trioxide. Because these oxides use to produce glass, silica, phosphorus, and boreal are typically required in large amounts.
Alumina(Al2O3) Ceramics
Ceramic Shop in Richmond VA made of alumina often have higher levels of chemical resistance, greater strength, and high temperature resistance. They can create via a method resembling sol-gel and then heated to a high temperature. Even though the final product has a rough surface, it has a solid polycrystalline structure. The component’s strength can increase by smoothing the surface with a coating of silica.
When subjected to high heat, alumina-zirconia ceramic fiber better maintains its mechanical qualities. And is frequently more beneficial in composite materials that must survive repeated exposure to higher temperatures. Similar characteristics exist in alumina-silica ceramic fiber and alumina-zirconia.
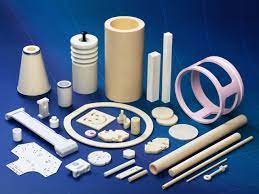
Ceramics containing beryllium oxide
Ceramics material made of beryllium oxide offer excellent thermal conductivity, high insulation, a low dielectric constant, little medium loss, and strong process flexibility. On sometimes, glass will include one of these ceramics. X-ray tubes constructs using glass that contains beryllium oxide, a material that can withstand x-rays. Both structural analysis and the treatment of skin conditions may do using it. Due to its durability and insulating qualities, beryllium oxide ceramics utilizes in high-power microwave and high-frequency transistor packaging.
zirconium ceramics
Zirconia ceramics provide good thermal insulation, low thermal conductivity, and a very high resistance to fracture propagation. Therefore frequently utilizes for their wire shaping and as protective coatings. As well as other medical equipment, they are employing in dentistry applications like as dental prosthesis. Ceramic knives frequently employ zirconia ceramics because they are less brittle than other ceramics.
Different Non-Oxide Ceramic Types
Ceramic non-oxides fill this demand as oxide ceramics aren’t always suitable for use in harsh environments or as a substitute in applications that must support heavy loads. Two often used ceramic non-oxide fibers with good heat resistance are silicon nitride and silicon carbide. Up until 2400 degrees Celsius, they do not deteriorate.
Non-oxide ceramic materials also have extremely strong oxidation, corrosion, and hardness resistance. Fiber production methods include spinning and curing the finished fiber using heat, as in pyrolysis and sintering.
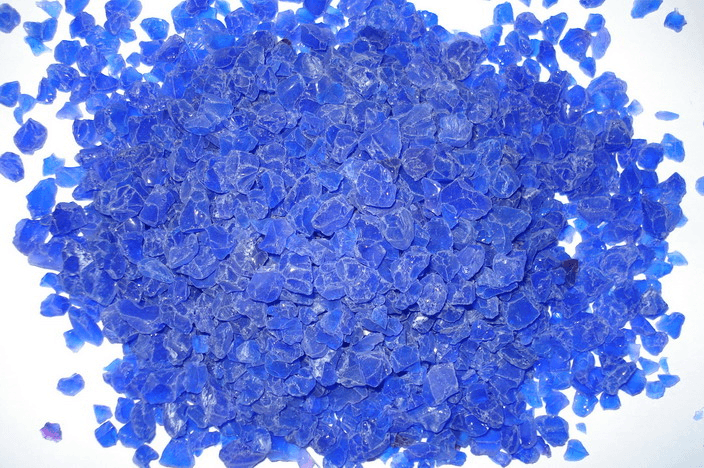
Ceramics made of silicon nitride
Aside from having a very low density, silicon nitride ceramics also offer a high fracture toughness, outstanding flexural strength, and great thermal shock resistance. One of three states of silicon nitride, green, biscuit, or completely dense, can machine. Ceramics material made of silicon nitride are used for spinning turbine blades, cutting tools, bearing balls and rollers, and bearings.
Ceramics with silicon carbide
Ceramic material made of silicon carbide are significantly lighter, tougher, and acid- and lye-resistant than conventional ceramics. Silicon carbide may produce in dense compacts using pressure less sintering methods, making it a common structural material. Because silicon carbide predominantly makes up of light components, these ceramics material are also lightweight. In addition, they exhibit great chemical stability, minimal thermal expansion, and good conductivity. They utilize for heat exchanger parts, suction box covers, seals, bearings, moving and stationary turbine parts, and ball valve parts.
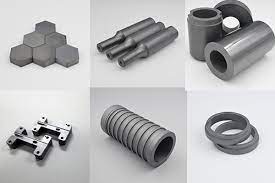
Ceramic Composites: Types
The physical or chemical characteristics of two or more of the constituent materials that make up a composite material differ considerably from one another. These ingredients come together to create a substance that differs from the sum of its parts in some ways. Composites vary from mixes and solid solutions in that the components are still easily identifiable inside the final structure. In a ceramic matrix, ceramic fibers finds in composite ceramics. Any ceramic substance may use to create the fibers and matrix.
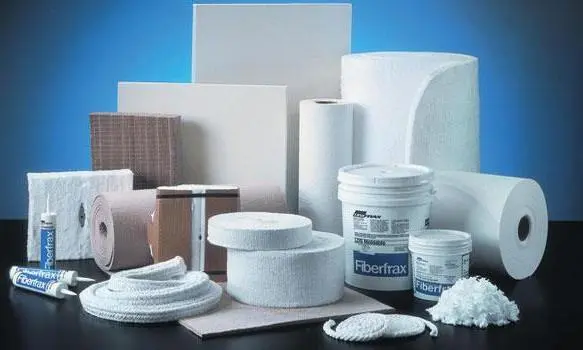
Ceramics with Fiber Reinforcement
Ceramic matrix-fiber composites, often known as fiber-reinforced ceramics, provide greater hardness and strength. The structure of the ceramic fibers, like that of traditional ceramics, can be polycrystalline. Additionally, they may be amorphous or have an uneven chemical make-up. Organic, metallic, or glass fibers cannot use because of the high process temperatures needed to create composite ceramics. It is only possible to employ fibers that are stable at temperatures exceeding 1000 °C, such as carbon, alumina, mullite, Sic, or zirconia fibers.
The main drawbacks of traditional ceramics, such as their brittleness, low fracture toughness, and limited thermal shock resistance, are not present in fiber-reinforced ceramics. They are therefore uses in industries that need high-temperature dependability and corrosion and wear resistance.
These applications comprise braking system components, burner, flame holder, and hot gas duct components, high temperature gas turbine components, heat shield systems for spacecraft, and so on. which endure intense heat stress and sliding bearing components that must have good corrosion and wear resistance when subjected to large loads.